Building for success: Inside story of the Academy dome
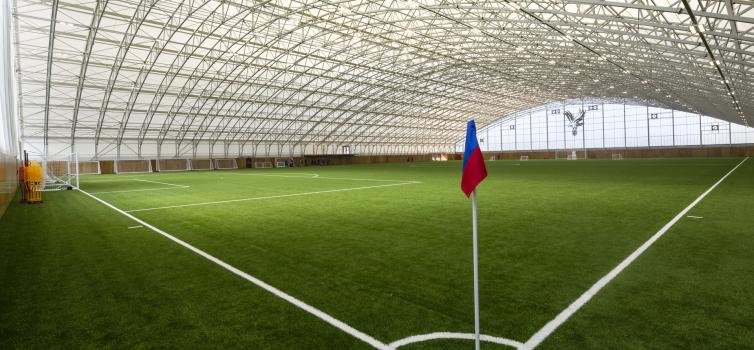
Crystal Palace's new indoor dome was opened in October 2021 as part of a £20m redevelopment of their Academy
Written by Simon Austin — August 16, 2024
The EPPP Academy system has transformed elite youth development in England, achieving its opening objective of producing more and better homegrown players.
Since EPPP was introduced, in 2012, there has been more than a trebling of full-time Academy coaches, a big increase in contact time with players and a doubling of Premier League minutes for homegrown English Under-21s. Perhaps most importantly of all, there has been success on the international stage for both the England youth and senior teams.
Another key component of EPPP has been a huge investment in buildings and infrastructure, which has exceeded £1 billion since 2012. Ged Roddy, the Premier League’s former Director of Football Development and the architect of EPPP, told TGG: “I think the Category One environment is world-leading in terms of the built infrastructure. I haven’t seen a network like it anywhere else in the world.”
Stepping inside an elite Academy is an impressive experience and the indoor dome is often the centrepiece. These indoor pitches ensure that young players are able to develop their technical skills even in the wet and cold of an English winter.
All Category One and Two Academies are required to have an indoor artificial surface measuring at least 60 x 40 yards (54.9 x 36.6 metres), while Category Threes must have access to an indoor surface of the same dimensions from at least November to April each year.

Collinson Tensile will be exhibiting at TGG Live 2024. To find out more about our industry-leading event at St George's Park on September 9&10, click below.
Crystal Palace opened their dome in October 2021 as part of a £20m Academy redevelopment that helped them gain promotion to Category One status. It has a full-sized 3G pitch with a viewing gallery. Stepping onto the indoor pitch in the dome, there are no obtrusive posts or pillars, natural light floods in and an intricate steel latticework curves above you.
Bournemouth had to commit to building an indoor dome before they were able to be promoted to Category Two in the summer of 2023. Their dome, which is 77m wide, 107m long and has a height ridge of 17m, has been in use since the start of this year.
Academy Manager Sam Gisborne said: “The facility is incredible. We use it every evening, have had zero issues so far and the players and staff love it.”
IDEAL FOR FOOTBALL
Preston-based Collinson Tensile built the domes at both Bournemouth and Palace and have become experts in the construction of indoor training facilities for football. Their steel-framed fabric buildings are supplied by Finnish company BestHall and were originally developed to provide cover from the snow in Scandinavia.
Over the last 22 years, the company have provided buildings for sports including football, rugby union, tennis, cricket, equine and even surfing instruction, but football now accounts for about 20% of their overall business.
“In the last five, six years we have started to see more investment coming in from the top tier clubs and, over the last couple of years, on the women’s side,” Director Dan Collinson told TGG.
“The bigger you go, the more these buildings become the only solution. Traditional buildings, where you have portal frames and a heavy gauge I-beam, become virtually impossible for a large span like a football pitch - because you would need internal posts for support, due to the weight of the steel.
“What we build is clear span. They’re a steel-framed structure, made from square hollow sections, with a lattice truss. You have a top cord and then a lower cord connected by diagonal steel braces. On full-size football pitches, the depth of that truss could be approaching 2m in height. They are comparatively light-weight, which is how we can go up to 100m clear span.”

To find out more about Collinson Tensile, or to book a call, click below
Another major benefit of these steel-framed fabric buildings is the natural light they provide.
“With traditional buildings, like a B&Q for example, you get pockets of light through the roof and skylights,” Collinson explained. “With ours, you get complete uniformity of light, not dark-light-dark-light, which is the best way to almost replicate outdoor conditions.
“It’s a nice environment to play sport and to work in. You have much higher lux levels, so in the daylight you’re not having to run artificial lighting at full power. That also gives environmental and economic benefits.”
Tensile means tensioned fabric, which is another big advantage.
“Once we’ve installed the fabric, it’s literally drum skin tight,” Collinson said. “You can walk on it, there is zero movement and it will still be like that in decades to come. Without movement, you don’t get wear and tear.
“The alternative would be wire ropes or cables in the tensioning, which will mean the building flexes and moves over the first two years and everything gets stretched. That means the membrane gets slacker and slacker and you have to either constantly keep going up to roof level to tension these things up, or else there’s wear and tear and damage.
“With ours it will keep performing. You can go and see one of our buildings that is 20 years old and it will still be performing. That’s what sets our system apart.”
CONSTRUCTION PROCESS
Collinson will typically be on site at an Academy for 16 weeks to complete a build.
“If you already have planning consent we could make a start in four months and you could be in and using the dome within eight months,” Collinson said.
The first stage is when the groundworks contractor goes in and constructs a reinforced concrete ringbeam around the perimeter of the building. Steel base plates are then cast into the concrete and stanchions and columns mounted on top.
“The finished building will weigh over 100 tonnes and that perimeter beam is like ballast,” Collinson explained.
“Our steel frames are pre-fabricated in the factory and then we have an automated shot-blasting and painting line, so they come to site with a powder-coated finish. Typically we would paint the frames white, to match the fabric covering that goes over the frame. You get a very nice clean crisp architectural finish.”
”In the cases of Bournemouth and Crystal Palace, about 50 articulated trailers delivered the steel to site. It was then assembled at ground level.
“We bring cranes in and lift the steelwork up from ground level in structural banks,” Collinson said. “The legs pivot into position and we work our way down the length of the building placing the frame into its final position.”
The fabric that covers the frame is a PVC-coated polyester membrane that is a maximum of 2mm thick.
“This is coated with a patented system called Precontraint, which is French,” Collinson said. “The yarns in the polyester have a bi-directional weave and the precontraint tensions the fabric in both dimensions, so you get this stability in the coating, which means it doesn’t stretch.
“That is providing the roof structure and keeping the wind and rain off.”
Bournemouth have been using their dome all year and aim to have the whole of their Canford Magna training and Academy complex open by the end of this year.
Project Manager Darren Booth said: “I did research into various options - seven companies in total - and my preference was for the Collinson system. If I were to do another project, the answer would still be the same: Collinson.”